Engineering & Design Automation is accelerating the outcomes for both manufacturers and customers in the wind energy industry.
Design automation can bring significant benefits to the wind turbine industry, especially when it comes to dealing with orders for distinct types of soils and terrains.
The layout of a wind turbine refers to the arrangement of its various components, such as the tower, blades, and nacelle. When designing and building wind turbines, the goal is to optimize their layout to achieve the most efficient and cost-effective energy generation.
By optimizing the layout of a wind turbine with mechanical configuration, it is possible to save time in the manufacturing and assembly process. Exemplifying, a well-designed layout can reduce the amount of material required for construction, which can decrease the time and cost of production. Similarly, an optimized layout can also make it easier and faster to assemble the various components of the turbine, which can result in considerable time savings for each order.
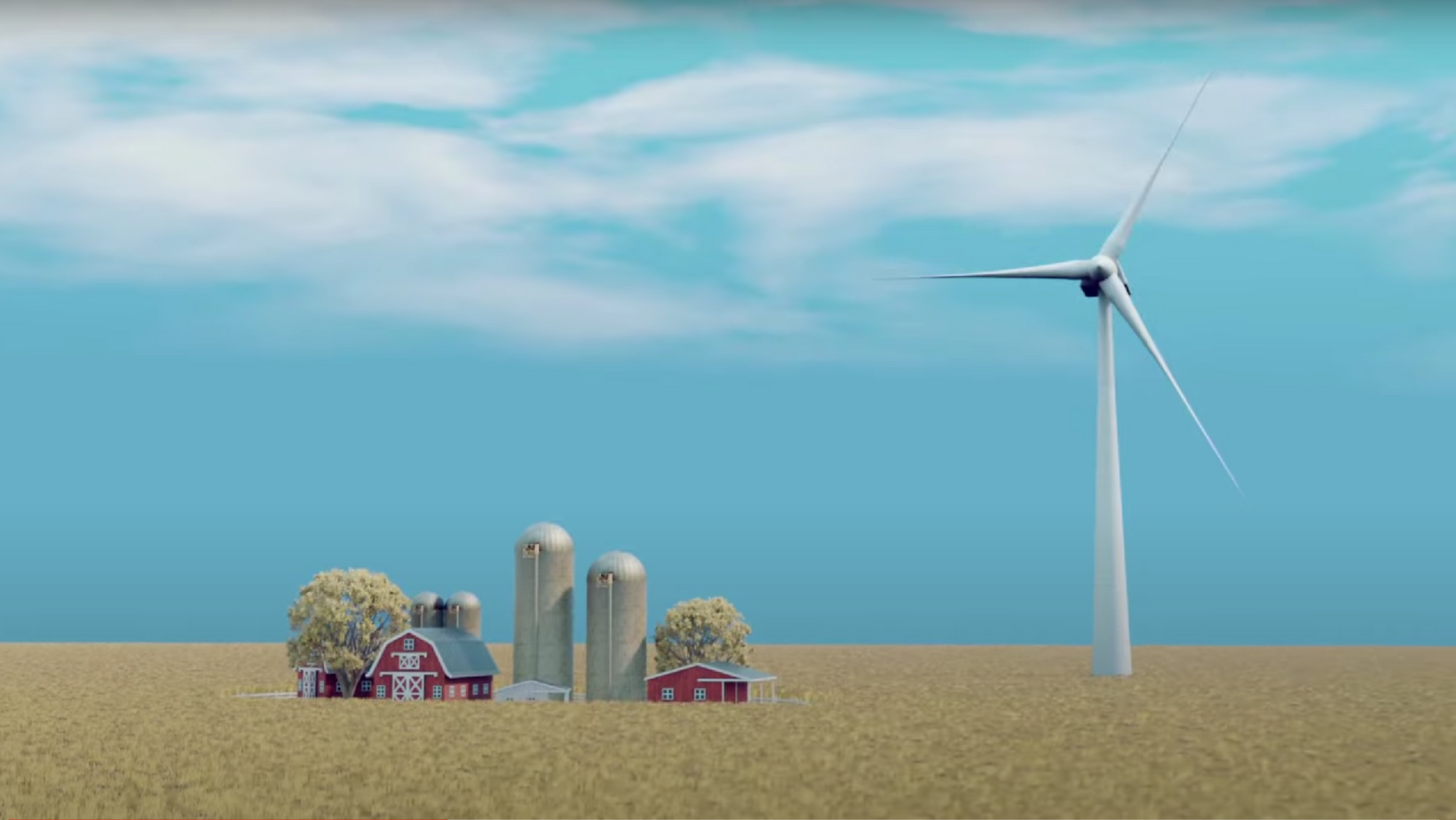
Optimizing the layout of wind turbines can lead to cost savings, improved efficiency, and faster construction times, all of which can be beneficial for wind energy companies and their customers.
Engineering & Design automation can bring significant benefits to the wind turbine industry, particularly when it comes to dealing with orders from different types of soils and terrains. By automating the design process, wind turbine companies can improve efficiency, reduce costs, and deliver more customized and accurate solutions to their customers in a faster way.
The colors on wind turbines can be customised based on client preferences and the surrounding environment. For land-based turbines in green landscapes, incorporating green elements helps them blend in with the surroundings. Red lines are often added for safety and visibility, marking moving parts. A configurator can be used to visualise and select colors, considering onshore or offshore placement. This customisation ensures visually appealing and safe integration of the turbines.
Another example of customisation, using DA (Design Automation) the automation software can take into account factors such as soil density, moisture content, and other geotechnical factors to determine the most appropriate foundation design for a particular location.
Watch in this DEMO wind turbines being configured and placed in different environments, showcasing their installation on various types of soils and terrains:
Our team has knowledge when it comes to wind turbines, and our main deliverable to clients in this industry is the rapid production of 3D models and comprehensive documentation. For instance, we provide detailed 2D drawings with all the necessary specifications and a complete bill of materials.
One of the benefits we already pointed to is the speed, by automating the design process, wind turbine companies can reduce the time it takes to design and build each turbine. This can be especially important when dealing with orders from different geographical locations, soil types and the terrain may trigger a unique design of components.
Highlighting the cost savings, design automation reduces the reliance on manual labor, resulting in fewer engineering hours. This enables wind turbine companies to offer more competitive prices to their customers or to have a higher profit margin.
To have a full overview of the value Design Automation brings you can check our 6 VALUE AREAS.
In conclusion, the wind turbine and wind energy sector can greatly benefit from engineering and design automation, as well as product configuration. The aforementioned benefits, such as cost savings, faster 3D modeling, comprehensive documentation, and increased competitiveness, demonstrate the positive impact of automation and standardization in this industry. Embracing digitalization and leveraging advanced technologies can drive efficiency, enhance productivity, and support the continued growth and sustainability of the wind energy sector.
Watch below a wind turbine being configured by our team using Tacton Design Automation Studio: