Parametrization in machinery manufacturing is a methodology that transforms the way machines are designed and configured. It involves incorporating adjustable parameters or variables within the machinery design, offering flexibility to adapt machinery to diverse specifications, production demands, or operational conditions. These parameters act as adjustable settings, allowing for easy modification without restructuring the entire system. This approach streamlines customization, enabling specific adjustments to be made efficiently, thereby amplifying adaptability across various manufacturing scenarios.
Comparing Parametrization, Modularization, and Standardization
While parametrization focuses on adjustable variables within the design, modularization involves building systems using standardized, interchangeable modules. Modularization enables the creation of complex structures from simpler, pre-built units, facilitating ease of assembly, repair, and customization. On the other hand, standardization revolves around uniformity in design and manufacturing processes, aiming for consistency and ease of production.
Each approach—parametrization, modularization, and standardization—offers distinct advantages. Parametrization stands out for its ability to fine-tune specific aspects of machinery without completely restructuring the entire system. Modularization excels in simplifying assembly and maintenance by utilizing interchangeable modules. Meanwhile, standardization ensures consistency and reliability in manufacturing processes.
The good news I have for you is that we have an experienced team in these three highly connected processes that will completely change your team’s work. Your team’s initial processes of modularization and standardization can be improved by our team or even initiated, if necessary, but it’s parametrization where we excel. Addressing various needs, the Scandinavian Digital team implements parametrization to completely transform your deals and orders, resulting in more sales and a stronger product. Ultimately, product quality is one of the key benefits in Design Automation.
Scenario: Creating a Parametrized Conveyor Belt System
In the video below, you’ll witness a scenario where a manufacturing company specializing in conveyor belt systems implements parametrization using Design Automation to adapt to diverse client requirements without the need for entirely new designs. This practical example illustrates how parametrization revolutionizes the customization process in conveyor belt systems used across various industries.
- Identification of Adjustable Parameters: The engineering team identifies crucial parameters that can be adjusted in the conveyor belt system. This could include variables such as belt speed, width, material composition, motor power, and sensor configurations.
- Designing a Parametrized System: Engineers design the conveyor system with these adjustable parameters in mind. They create a system that allows for easy modification of these key variables without requiring an entire system overhaul.
- Adaptability and Customization: When a new client order comes in with specific requirements, such as a conveyor belt for heavy-duty materials or delicate items, the team uses the parametrized design to swiftly adapt the system. For heavy-duty materials, they may adjust parameters like belt width, stiffening, and motor power for efficient handling. Conversely, for delicate items, parameters such as reduced belt speed, softer materials, and adjusted sensor sensitivity are modified without redesigning the entire system.
- Efficiency and Cost Savings: The parametrized design approach significantly reduces lead time and costs typically associated with creating customized systems for each client. It streamlines the manufacturing process, ensuring efficient responses to various client needs.
- Scalability and Future Adaptation: As the company’s clientele expands or industry demands change, the parametrized design acts as a flexible base for further modifications or scaling. New parameters can be introduced or adjusted to meet evolving requirements.
- Demonstrating Flexibility and Versatility: The video demonstration showcases how parametrization enables the manufacturing company to efficiently address different client needs across various industries. It highlights the system’s flexibility in adapting to diverse specifications without compromising quality or efficiency.
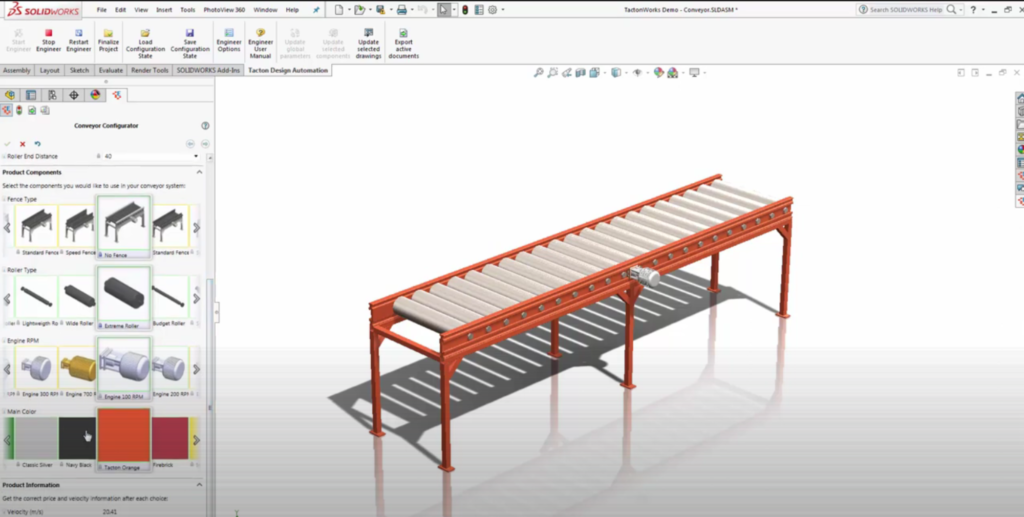
The Game-Changing Impact of Parametrization for Machinery Manufacturers
Parametrization emerges as a game changer for machinery manufacturers dealing with complex and varied products. Its adaptability allows for swift adjustments in machinery to accommodate varying requirements or changes in production needs. This capability significantly reduces design iteration time and improves responsiveness to market demands.
The flexibility of parametrization empowers manufacturers to tailor machinery to specific client requirements without extensive redesigning, thereby minimizing engineering lead time. Moreover, it optimizes resource utilization by enabling efficient reuse of existing designs with parameter adjustments, saving both time and costs associated with creating new systems from scratch.
Industries embracing parametrization, such as automotive, aerospace, and semiconductor manufacturing, are leveraging its advantages to drive innovation and rapid adaptation. In contrast, sectors yet to adopt this methodology may face limitations in responding promptly to market dynamics or incorporating cutting-edge technologies into their machinery.
Talking about innovation as a benefit is precisely what companies need to stay ahead of the competition. Once these implementations prioritize a more streamlined process, efficiency is ensured, with an emphasis on maintaining overall efficiency as the primary objective. Parametrization presents a forward-looking approach in machinery design offering a blend of adaptability, efficiency, and agility that paves the way for competitiveness and leadership in the market.